Evolução da manutenção industrial da origem até o presente
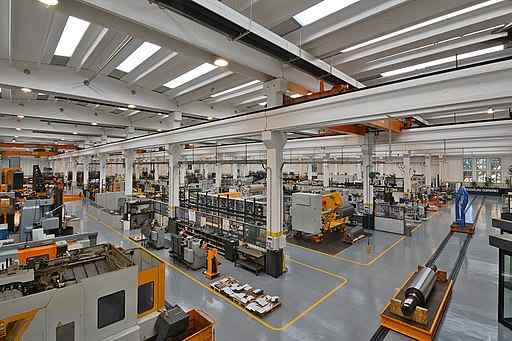
- 1704
- 326
- Melvin Mueller
O Evolução da manutenção industrial Começou a ser mais significativo após o primeiro da Guerra Mundial, o estágio em que as máquinas tiveram que trabalhar com capacidade máxima e sem interrupções. Anteriormente, o trabalho era o que realizava quase 90% do trabalho, em comparação com os 10% estimados que fizeram as primeiras máquinas.
A manutenção industrial se origina ao mesmo tempo em que as máquinas começaram a ser implementadas para a produção de bens e serviços, no início do século 19. Como uma característica comum para todas as suas fases de desenvolvimento, a necessidade de torná -la cada vez mais especializada é apresentada.
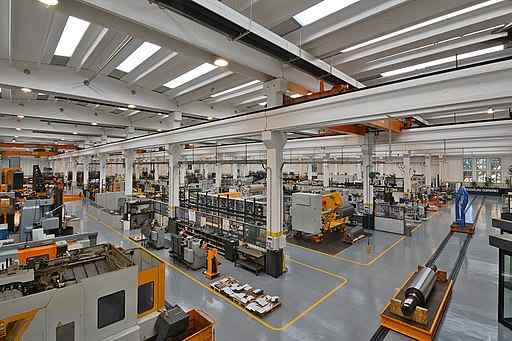
Manutenção industrial é o conjunto de medidas técnicas organizacionais, que podem ser elaboradas anteriormente, que visa sustentar a funcionalidade do equipamento e garantir um estado ideal de máquinas ao longo do tempo.
Entre os objetivos de manutenção industrial podem ser mencionados: conservar a capacidade de trabalho das máquinas, reduzir paradas imprevistas, contribuir para o aumento da produtividade, conservar em perfeitas condições os meios de produção com um custo mínimo.
Através de planos de manutenção industrial, é destinado a sua vida útil.
As tarefas de manutenção industrial não são exclusivas de equipamentos e máquinas, mas de qualquer instalação fixa ou móvel, serviços industriais, comerciais ou específicos, ou seja, qualquer tipo de bem produtivo.
[TOC]
Estágios de sua origem até o presente
Primeira geração: da Revolução Industrial até 1950
Corresponde a Manutenção corretiva total, em que se espera que algum colapso prossiga com a respectiva reparação. Esta fase é geralmente identificada antes de 1950 e é a etapa mais longa, porque começa com a revolução industrial. Os custos de manutenção costumavam ser bastante altos e o tempo de desemprego para resolver os problemas foi prolongado.
Com a implementação da produção serial, após a Primeira Guerra Mundial, as fábricas começaram a estabelecer programas mínimos de produção e a necessidade de formar um equipamento que se concentrava em manter as máquinas das linhas de produção e diminui para a letra possível, a parada da parada.
Pode atendê -lo: automação industrialParalelo à área de produção e depois à manutenção focada em reparar falhas corretivas ou de urgência. Além disso, tarefas de prevenção foram atribuídas para evitar falhas.
A manutenção corretiva foi caracterizada pela apresentação de altos custos de mão -de -obra e altos custos de oportunidade, uma vez que a disponibilidade do sobressalente deve ser imediata para poder abordar qualquer dano que estivesse registrando.
Entre as desvantagens mais óbvias estão a afetação da qualidade devido ao desgaste progressivo do equipamento, o risco de não ter a disponibilidade de substituição, o que significava grandes custos, os tempos mortos por falhas repentinas e o risco de que outros problemas pudessem ser gerados em paralelo.
Segunda geração: de 1950 a 1970
O trabalho de manutenção preventiva já estava sistematizado para o advento da Segunda Guerra Mundial. E alguns anos depois, surgiu a American Quality Control Society, o que ajudou a realizar o estudo estatístico do trabalho, melhorando também a qualidade dos produtos obtidos.
A segunda geração se concentra no mantimento preventivo de avarias, os trabalhos cíclicos e repetitivos são realizados com uma certa frequência para a conquista do referido objetivo. Esta fase se estende até o final dos anos 70.
Nele, as substituições preventivas começam a ser feitas, à medida que a relação entre o tempo de vida do equipamento e sua probabilidade de falha é descoberta.
A manutenção preventiva tem várias modalidades: pode ser um processo a ser realizado periodicamente, geralmente com um intervalo de tempo de 6 a 12 meses. Também pode ser agendado de acordo com os fabricantes ou pelos padrões estabelecidos pela engenharia.
Outra modalidade pode pretender implementar melhorias no processo e, embora não tenha uma frequência estabelecida, é um redesenho otimizar o processo. Finalmente, há manutenção autônoma, realizada pelo operador com atividades simples ou de rotina.
Terceira geração: de 1980 a 1990
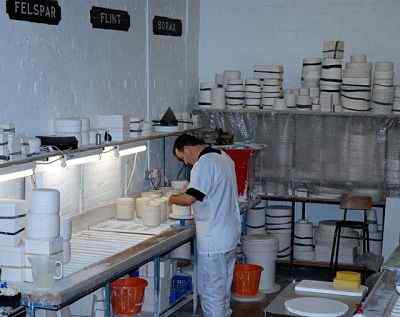
A manutenção é implementada por condição, ou seja, a que depende do monitoramento de parâmetros, dependendo de qual substituição ou recondicionamento de máquinas será realizada.
Pode atendê -lo: telégrafo: história, invenção, evolução, como funcionaEste trabalho é possível graças à disponibilidade de equipamentos confiáveis de inspeção e controle, que permitem conhecer o estado real do equipamento por meio de medições periódicas.
É a hora de Manutenção preditiva, que consistia na detecção precoce de sintomas incipientes de problemas futuros. Estudos de efeito causam-se geralmente para descobrir a origem das falhas. Um elemento diferenciador nesta fase é que eles começam a se envolver nas áreas de produção na detecção de problemas.
Uma das grandes vantagens da manutenção preditiva é a possibilidade de monitoramento e registro de falhas, por isso será mais fácil agendar reparos futuros e menos intervenções de pessoal de manutenção serão registradas.
Quarta geração: de 1990 até os dias atuais
O início desta fase é geralmente identificado nos anos 90, quando as empresas americanas já haviam incorporado em sua dinâmica o conceito de qualidade total que as indústrias japonesas estavam promovendo a partir de 60. Total Quality Management (TQM) procurou criar consciência de qualidade em todos os processos da organização e nas pessoas que trabalharam nele.
A quarta geração corresponde a Manutenção Produtiva Total que se inspira nessa filosofia de origem japonesa que busca excelência ou dita em uma frase: obtenha o máximo com qualidade aceitável, pelo menos um custo possível, em um sentido perolado e abrangente. Para isso, pequenas tarefas de manutenção, como ajuste, inspeção, substituição de peças, são realizadas e interação contínua com o gerente de manutenção.
O programa se concentrou no fator humano de toda a empresa para a qual as tarefas de manutenção preventiva são atribuídas para maximizar a eficácia das mercadorias. Ele supõe três princípios: sempre mantenha as instalações em boas condições, concentre -se em aumentar a produtividade e envolver a totalidade da equipe.
Esta é a fase dos sistemas de melhoria contínua e é caracterizada pela implementação de ações para a melhoria e monitoramento das ações. A manutenção se torna um benefício, e não um mal necessário, e é assumido como um compromisso por todos os departamentos da organização.
O objetivo é alcançar a eficácia total do equipamento que implica eficiência econômica por meio da disponibilidade, desempenho máximo e produtos de qualidade.
Pode atendê-lo: sistema humano-máquina: características e exemplosAlém disso, três outras ferramentas são geralmente implementadas: engenharia de risco que envolve determinar as consequências de falhas aceitáveis ou não; a análise de confiabilidade que se refere à identificação de tarefas preventivas viáveis e lucrativas; A melhoria da manutenção que consiste em reduzir os tempos e os custos de manutenção.
Nesta fase, houve mudanças importantes na legislação sobre segurança e higiene no trabalho, além de práticas mais amigáveis para o meio ambiente. Portanto, dispositivos de purificação, plantas de extração, atenuação de ruído, equipamentos de detecção, controle e alarmes começaram a ser implementados.
Hoje, especialistas no campo estimam que os custos de manutenção sofrerão um aumento progressivo que levará os setores a gerar produtos de manutenção mais confiáveis e fáceis.
Importância da manutenção
A manutenção industrial deixou de ser um mal necessário para o qual vários departamentos de uma organização estão comprometidos e envolvidos. Isso ocorre basicamente porque a verdadeira importância do gerenciamento eficaz de falhas ou problemas de equipamento e instalações foi reconhecido, o que pode afetar qualquer um dos estágios de produção de bens ou serviços.
Deve -se notar que a importância da manutenção industrial está no seguinte:
- Evita acidentes de trabalho e aumenta a segurança das pessoas.
- Reduz as perdas devido a paradas de produção.
- A gravidade das falhas que não são evitadas diminuem.
- Evita danos que podem ser irreparáveis em equipamentos ou instalações.
- Garante o desempenho aceitável do equipamento.
- Permite documentar os processos de manutenção necessários para cada máquina.
- Prolonga a vida útil de equipamentos ou mercadorias.
- Retém bens produtivos em condições operacionais seguras e pré -estabelecidas.
- Melhora a qualidade da atividade.
- Permite a preparação adequada do orçamento, ajustada às necessidades da empresa.
Referências
- Muñoz Abella, M. (2003) Manutenção industrial. Madri: Universidade de Carlos III de Madrid. Área de Engenharia Mecânica.
- Mora Gutiérrez, A. (2009). Manutenção: planejamento, execução e controle. México: editor Alfaomega Grupo.
- Manutenção industrial. (s.F.). Recuperado de Ecurido.Cu
- Netos. História de manutenção. (2009, 27 de maio). Recuperado da manutenção industrial2009.Blogspot
- Villada, "Manutenção como uma estratégia competitiva", Rev. FAC. Ing. Univ. Antioquia, não. 17, pp. 7-13, 1998.
- A evolução da manutenção industrial: Blog: ATS. (2019, 26 de julho). Recuperado de AdvancedTech.com
- « Estrutura de nitrato de sódio (nano3), propriedades, usos, riscos
- Conceito de distância euclidiana, fórmula, cálculo, exemplo »